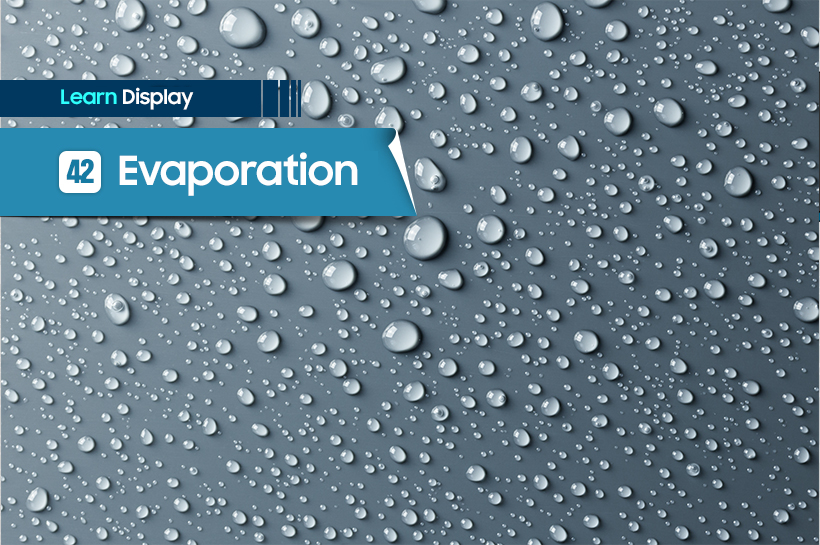
Evaporation refers to the thin-film deposition process for the material of the evaporant on the display substrate. In other words, it heats and evaporates the compounds of the material meant for deposition within a vacuum chamber.
The evaporation process is in use for color patterning in OLED displays. OLED manufacturing is generally divided into five stages: ① Low Temperature Polycrystalline Silicon (LTPS) process → ② Evaporation process → ③ Encapsulation process → ④ Cell Cutting process → ⑤ Module process
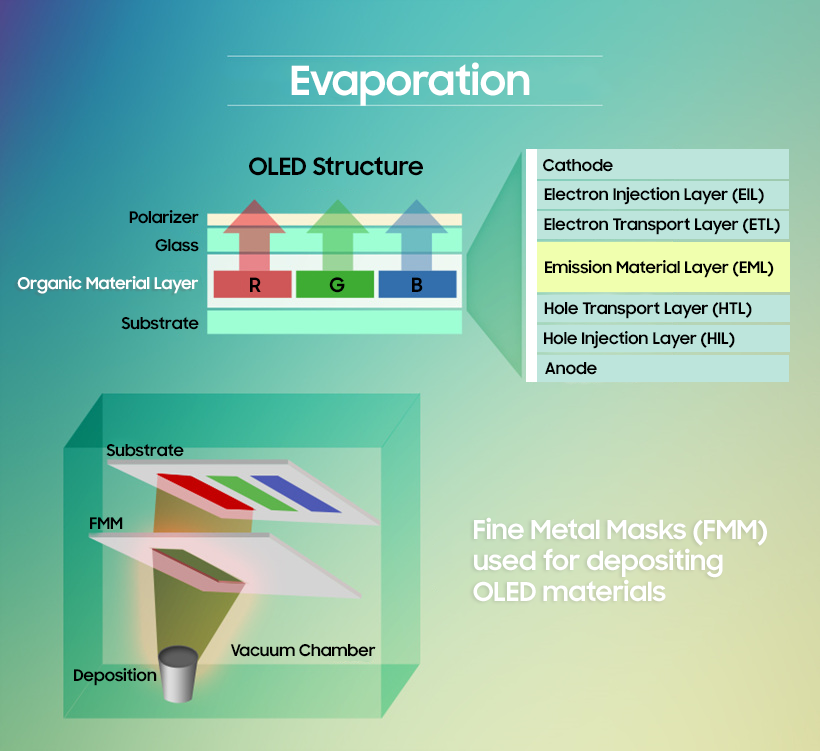
The evaporation process is one of the key processes in producing self-emitting OLED pixels. The RGB light emitting organic material layer is placed on top of the substrate. This organic material layer consists of an emissive layer and additional layers that support light emission. Hole Injection Layer (HIL) and Hole Transport Layer (HTL), Electron Injection Layer (EIL) and Electron Transport Layer (ETL) enable easier injection and transport of holes and electrons into Emissive Layer. Layering these multi-organic layers into one organic material layer is what makes the evaporation process important.
In order to initiate the evaporation process, we need to place the Low Temperature Polycrystalline Silicon (LTPS), which serves as the base for deposition, in the vacuum chamber. Then we put a fine metal mask (FMM) on the LTPS.
A mask is a metal sheet with tiny openings meant for depositing materials in specific areas. A fine metal mask (FMM) is used to deploy the RGB colors of organic materials in the OLED display manufacturing process by subdividing small pixels.
By heating and evaporating the deposition material, its molecules pass through the FMM openings and land upon designated areas on light-emitting organic material layer and cathode layer fabrication.