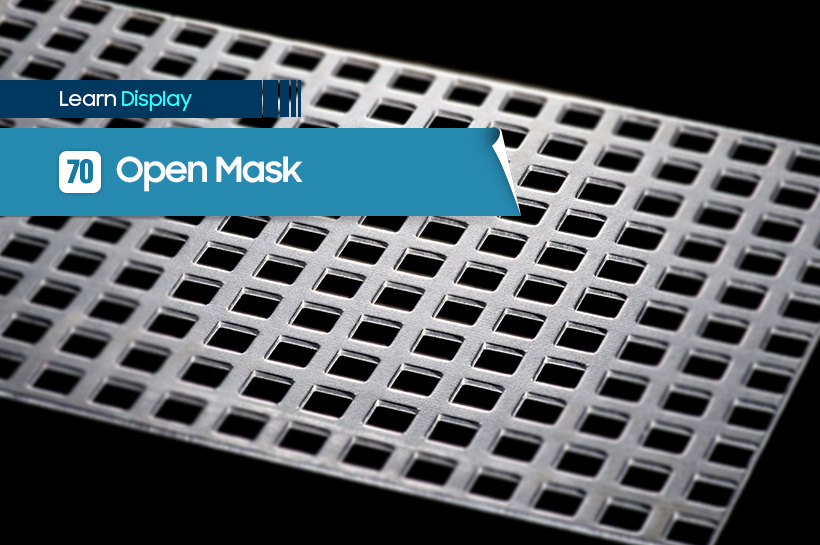
An open mask (OM) refers to a thin plate that ensures evaporation in specific target areas on an OLED display panel. It is used in the evaporation process required to create an emission material layer (EML) on top of the completed backplane during the display manufacturing process.
There are two types of masks used in the evaporation process: An open mask (OM) and a fine metal mask (FMM). An open mask was deposited on the front of the display without any covers on the active display area. It is also used during Electron Injection Layer (EIL) and Hole Transport Layer (HTL) evaporation process or during a single color light-emitting material deposition on an emission material layer (EML).
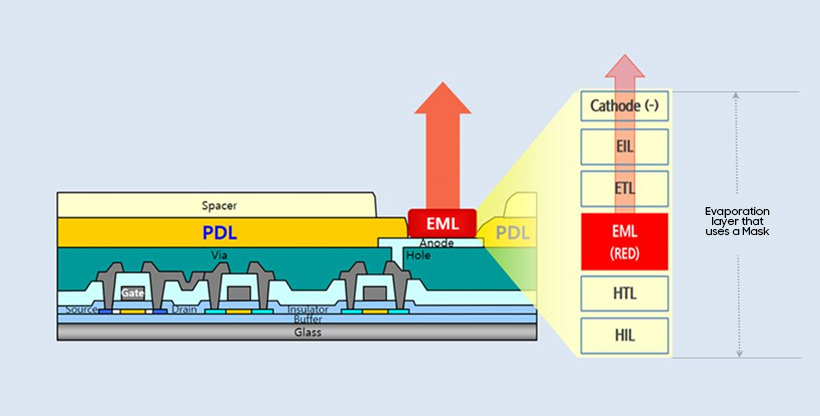
On the other hand, the fine metal mask (FMM) has super fine holes designed to separate the colors of the sub-pixels in the EML. As the sub-pixels require several stages of the evaporation process, accurate alignment of the mask is crucial; therefore, the FMM is a more complex technology compared to the open mask (OM).
When the EML is deposited on an OLED display using an OM, the EML can only emit light of a single color, and therefore, a separate layer is needed to produce colors, such as a color filter (C/F). In contrast, a color filter is not required when a FMM is used to form the EML that emits light in RGB colors. In other words, while the FMM technology is more challenging to implement, it is better than the OM method in terms of luminous efficacy as it removes the need for a filter that interrupts light emission.
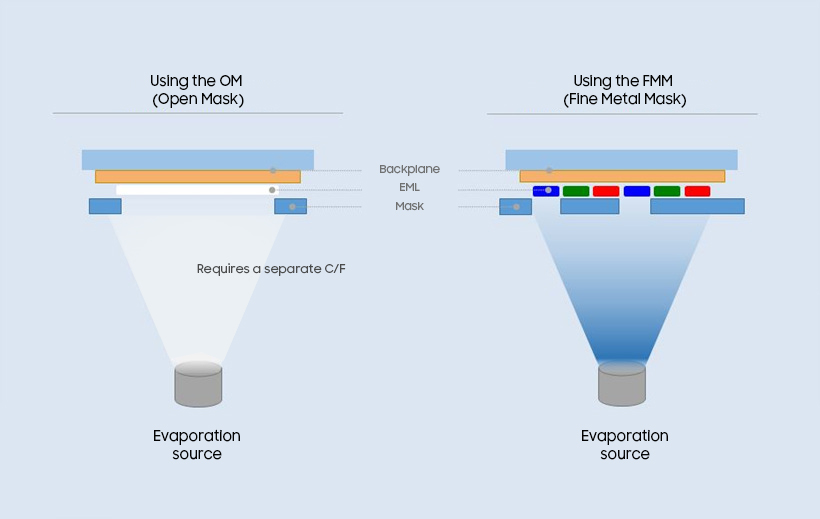
Because an open mask is made of metal and the evaporation process is conducted at high temperatures, thermal expansion due to the increase in the temperature may result in the misalignment of pixels. Special metal is actively used instead to minimize the impact of thermal expansion.
The key methods of fabricating a mask include photolithography/etching of a metal plate, laser processing, and mechanical cutting.