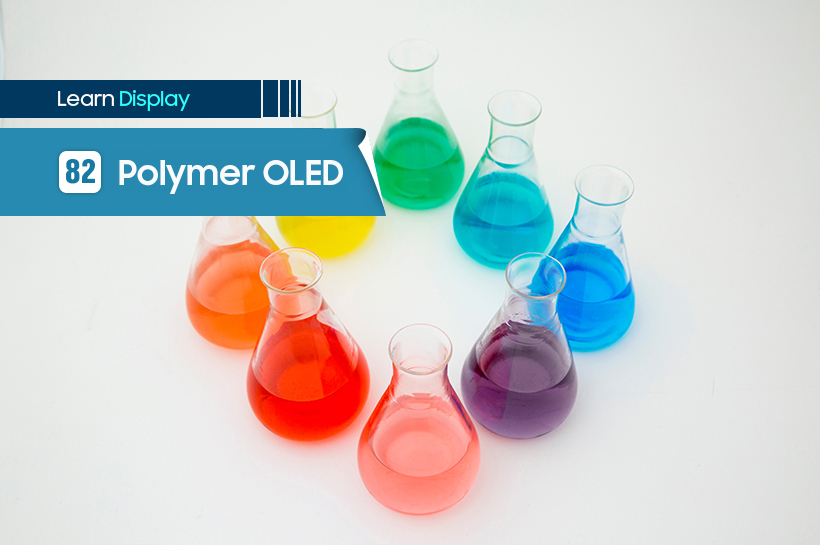
OLED emissive materials used in displays are categorized into a ‘small molecule’ and a ‘polymer’ group. First discovered at Cambridge University in 1990, polymers refer to materials with a molecular weight over 10,000 g/mol. Polymers are heavier and more complex than small molecules. Therefore, the inkjet printing process using solvents instead of the evaporation process is more ideal for polymer materials.
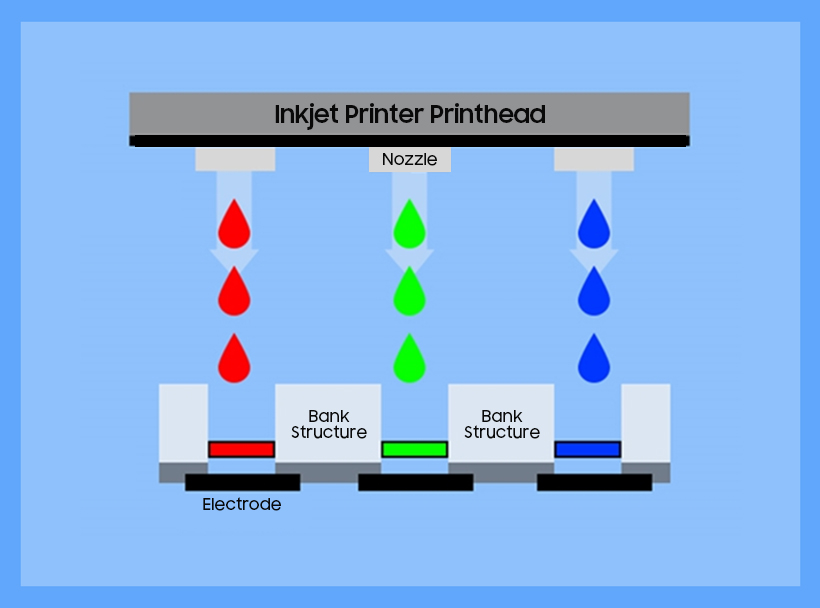
The inkjet printing process for OLED is as follows: Ink formulation → Deposition → Annealing. In order to utilize polymer materials as OLED display pixels, they first need to be formulated into inkjet ink. For every red, green, blue light emitting material, it is readily soluble by solvents and dissolved into ink. Once the ink is prepared, it is placed in the printer nozzle and deposited in precise locations for display pixel formation. Ink is dried, cooled down, and turned into a thin-film pixel after annealing.
Unlike small molecule OLEDs that use fine metal mask (FMM), Polymer OLEDs offer higher yields for material consumption and atmospheric pressure without a vacuum chamber.