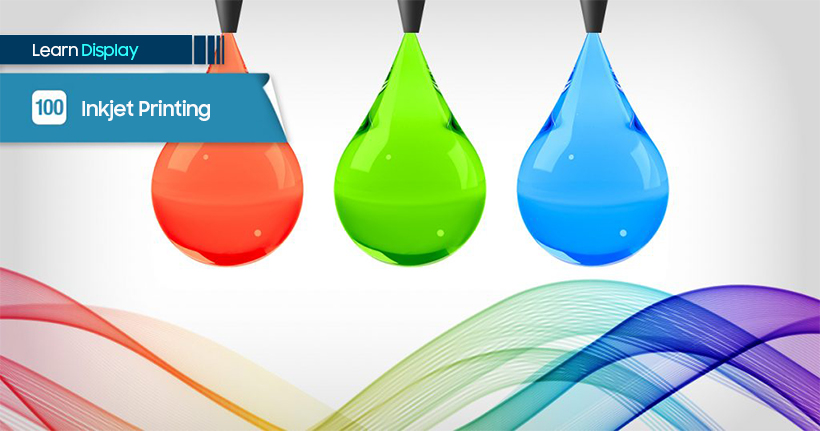
In the context of display production, inkjet printing refers to the technology that is used to manufacture OLED display pixels, by spraying a solution through the nozzle found on the inkjet head. Just as a printer sprays ink onto a piece of paper, inkjet printing sprays OLED ink, which is only a few dozen picoliters (one picoliter is one trillionth of a liter) in size, to mass-produce displays.
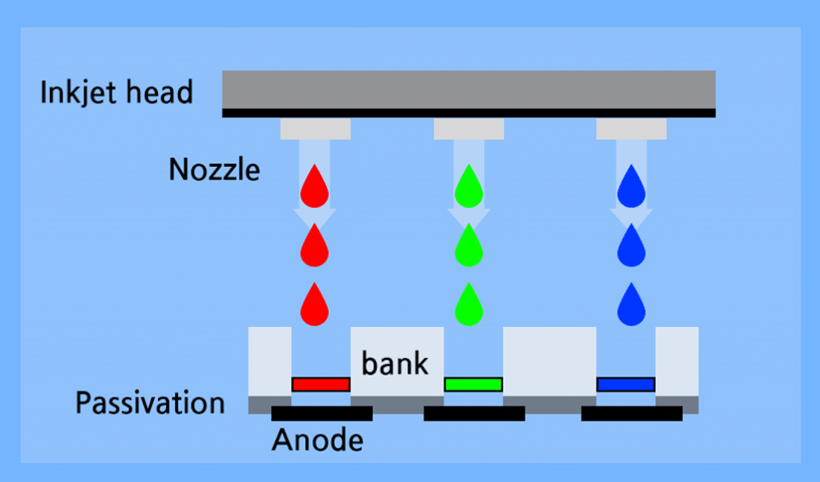
In the inkjet printing process for OLEDs, the organic material must be dissolved by a solvent to create a soluble OLED solution. It is similar to dissolving salt (organic material) in water (solvent). The ink that contains the dissolved organic material is then sprayed through the nozzle located on the inkjet head onto the display substrate, specifically into the space between the banks that separate the R, G, and B colors. After the ink is injected, it is dried to remove the solvent, leaving only the organic material that becomes the pixels for OLED to emit light.
Unlike the evaporation method where the organic material is evaporated in a vacuum, inkjet printing allows the production of pixels even under normal pressure or in a low-level vacuum. By injecting an appropriate amount of organic material, inkjet printing also increases the efficiency of raw material usage. Moreover, compared to the evaporation method, inkjet printing is more suitable to produce large display panels from a larger mother glass. Despite all these strengths, inkjet printing still faces challenges to commercialization, including the coffee ring effect and difficulty in maintaining a consistent thickness and density of the organic material. However, industry experts expect that overcoming such challenges through research and development of materials and process technology will usher in a new era of using inkjet printing to manufacture OLED displays.