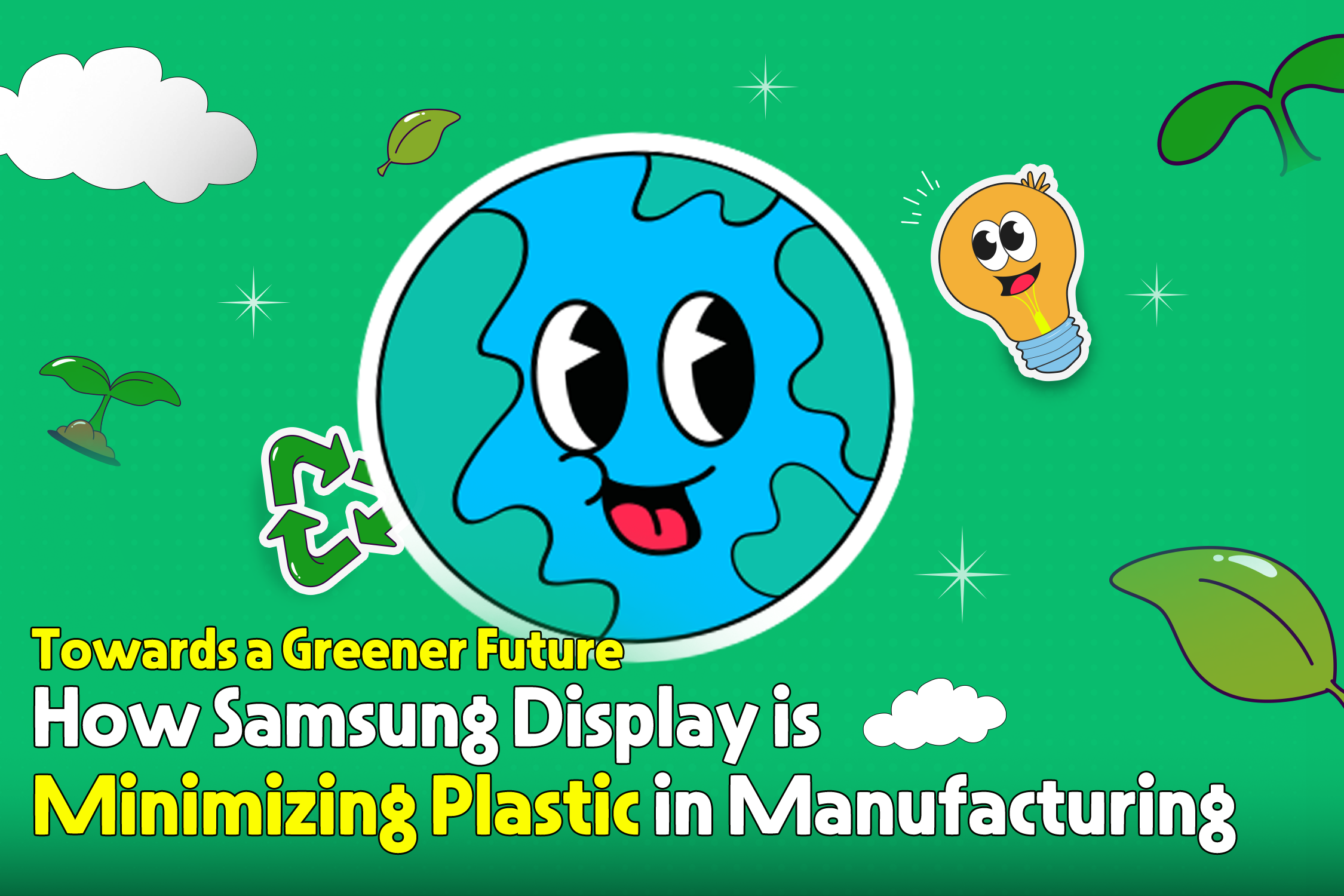
Everyone remembers what April 22nd is all about - it's Earth Day, a day to remind us of the importance of protecting our planet. Earth Day was founded by citizens in the United States in 1969 after a devastating oil spill off the coast of California raised national concern for the environment. Today, it’s a global day of action for environmental protection. In Korea, Earth Day marks the beginning of “Climate Change Week,” a one-to-two-week period filled with environmental campaigns such as energy-saving initiatives and lights-off events that raise awareness around greenhouse gas reduction and low-carbon lifestyles.
Plastic discarded 100 years ago, still rotting?
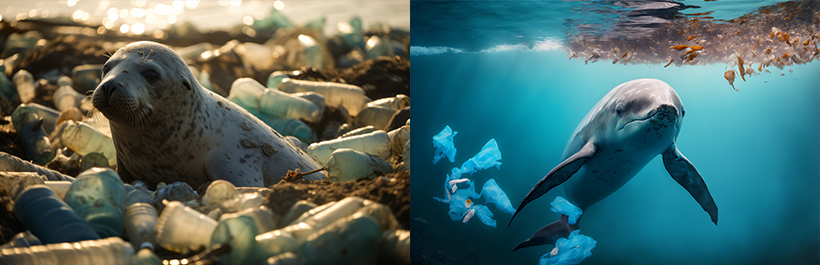
The sight of turtles entangled in plastic or dolphins harmed by ingesting it has sadly become all too familiar. According to the UN, global plastic production is accelerating, with annual output expected to reach 11 million tons by 2050. The vast majority of these plastic products are single-use, eventually finding their way into lakes, rivers, and oceans, where they cause serious damage to ecosystems. Since plastic takes centuries to decompose, even some of the earliest plastics still linger in the environment today.
To address this pressing issue, governments, businesses, and individuals around the world are stepping up to reduce plastic use. At Samsung Display, efforts are being made across products, manufacturing, and daily operations to minimize plastic consumption. Today, we’d like to introduce some of the key innovations in our manufacturing processes that are helping us move toward a more sustainable planet.
How could we reduce the usage of “Tray,” a must-have in manufacturing process?
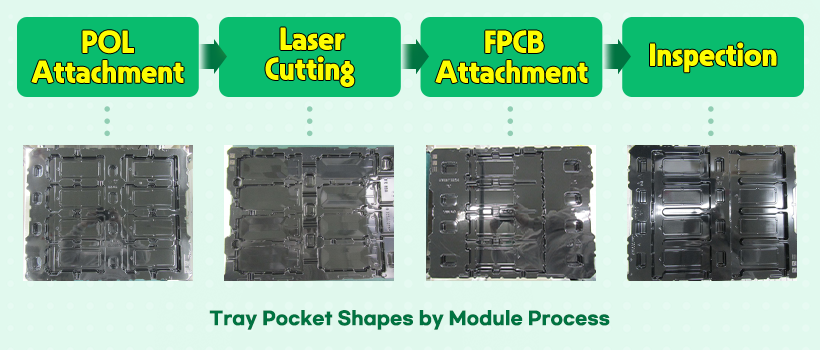
Display panels undergo a series of complex manufacturing steps, and plastic trays are used to safely transport products between these stages. These trays are designed to be lightweight yet strong, with custom-fitted pockets that secure each panel. However, each time a product design changes, a new set of trays must be made to fit the new specifications.
This issue becomes more complex in the final module stage, where components such as polarizers (POL) and FPCBs are attached—altering the panel’s shape. Though these trays are reusable to a degree, many are discarded due to wear or damage over time.
Universal Trays: One Solution Across Many Processes
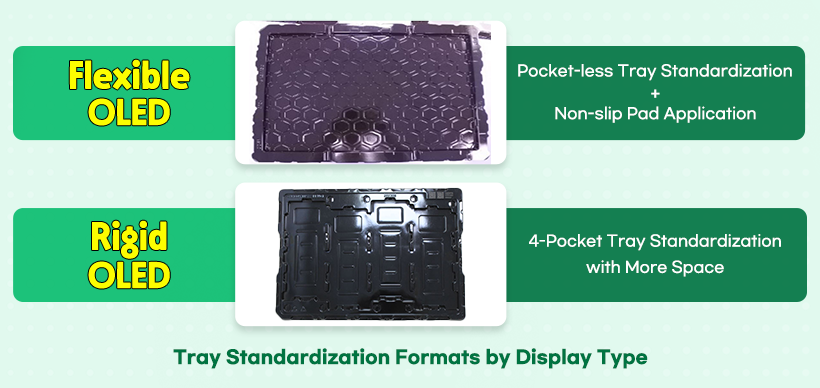
To address this challenge, Samsung Display formed a task force to standardize trays across processes. For flexible OLEDs, we developed pocket-less trays with non-slip pads that secure panels without the need for molded pockets, allowing us to use a single tray design across all module processes.
For rigid OLEDs, which use glass substrates and are heavier, a larger 4-pocket tray was introduced to prevent damage during transport. IT displays, which tend to be larger in size, have also adopted the pocket-less tray format to create process-wide universal trays.
Results That Matter: A 60% Cut in Flexible OLED Tray Usage
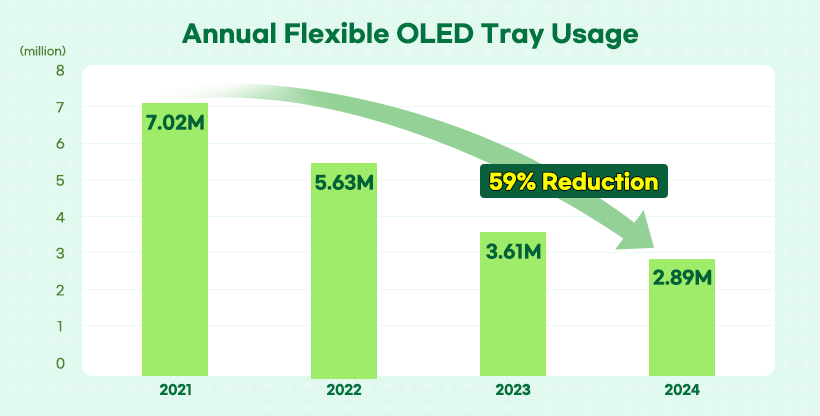
The transition to pocket-less trays for flexible OLED production began in 2022 and was fully implemented by 2024. That same year saw the rollout of universal trays for IT and rigid OLED products as well, gradually expanding their territory in the manufacturing process.
Thanks to these innovations, Samsung Display significantly reduced its tray usage. In 2021, Samsung Display used about 7.02 million trays annually for flexible OLEDs. By 2024, that number dropped to 2.89 million—a reduction of nearly 59%. With each tray weighing approximately 330 grams, this translates to 1,360 tons of plastic saved over three years.
Closing the Loop: Recycling Waste Trays into New Ones
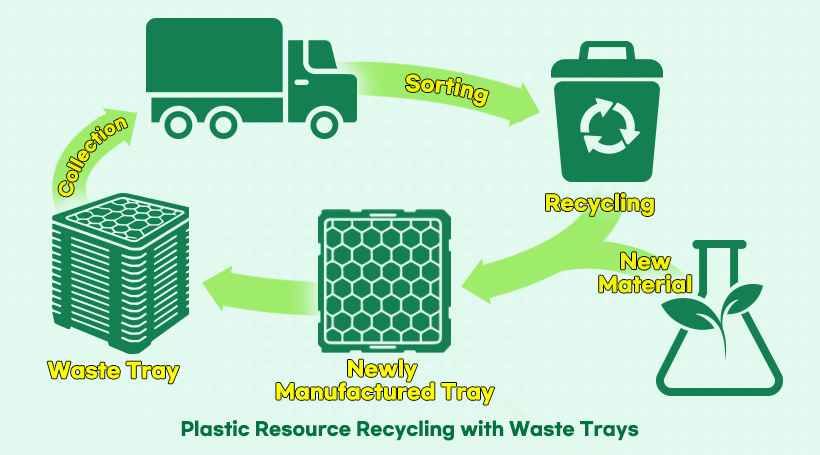
Reducing consumption isn’t the only goal—Samsung Display is also closing the loop through recycling. Since 2022, we have collected discarded trays from domestic FABs and reused them as raw material to create new trays. These eco-trays are made using about 56% recycled plastic, blended with new material, and are reused in display panel production. This practice is expanding globally, with overseas sites using up to 40% recycled content in tray manufacturing—further reducing our plastic footprint.
A Culture of Sustainability: Plastic Reduction Beyond the Factory
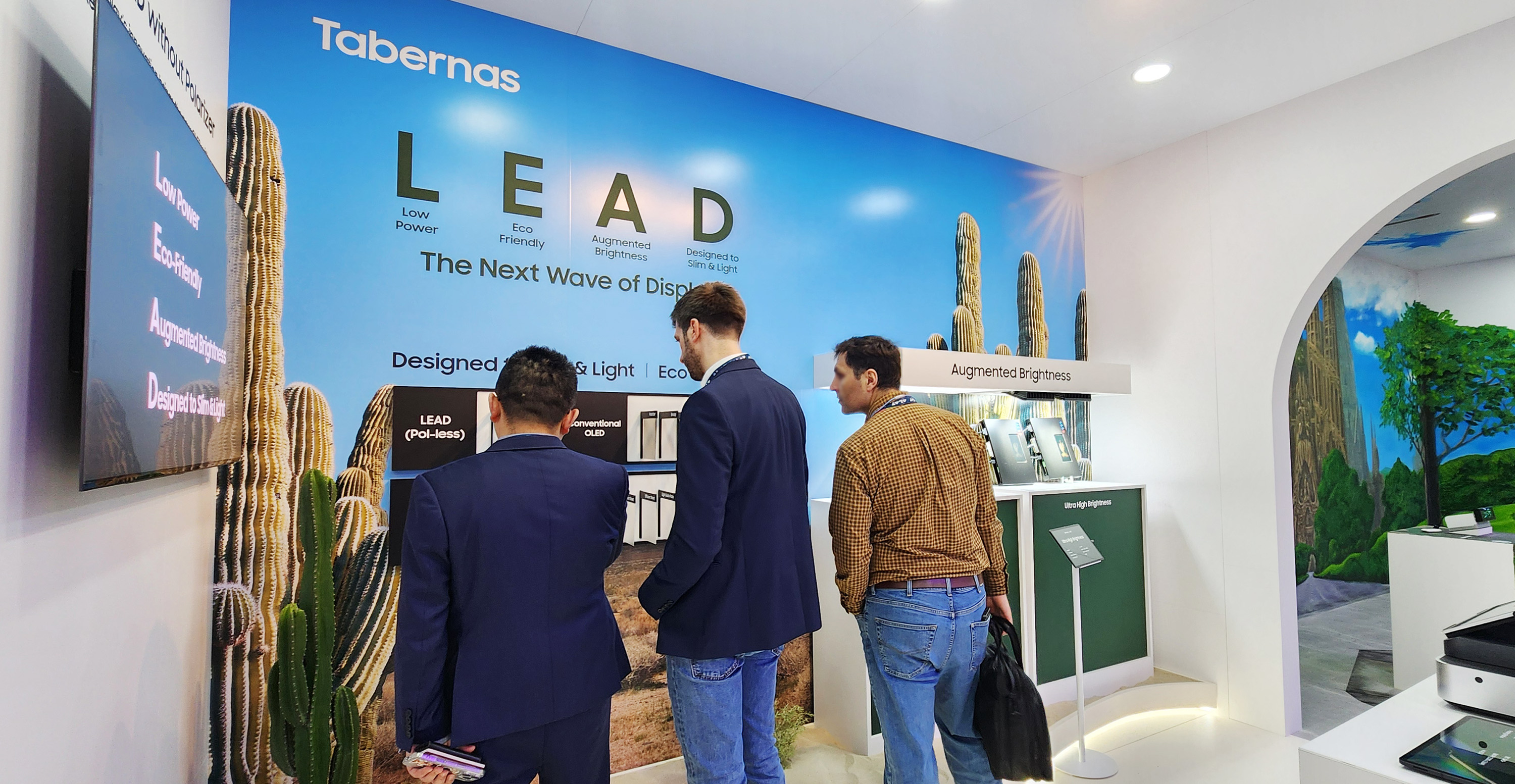
Samsung Display’s efforts to reduce plastic extend beyond the manufacturing floor. In our display products, we developed and applied a proprietary technology called ‘LEAD,’ which eliminates the polarizer - an opaque plastic sheet that blocks external light reflection - while improving light efficiency and lowering power consumption. Assuming one million units are produced annually, this technology can reduce plastic usage by approximately 79 tons per year.
We are also reducing plastic use in daily workplace practices. Employees use eco-bags instead of disposable plastic bags, and on rainy days, umbrella bag dispensers have been replaced with umbrella dryers. In our on-site cafés, reusable cups and personal tumblers are encouraged, and takeout containers in our cafeterias have been switched to reusable ones.
Small actions lead to meaningful change. Samsung Display is committed to thinking about the planet—not just on April 22, but every day of the year.