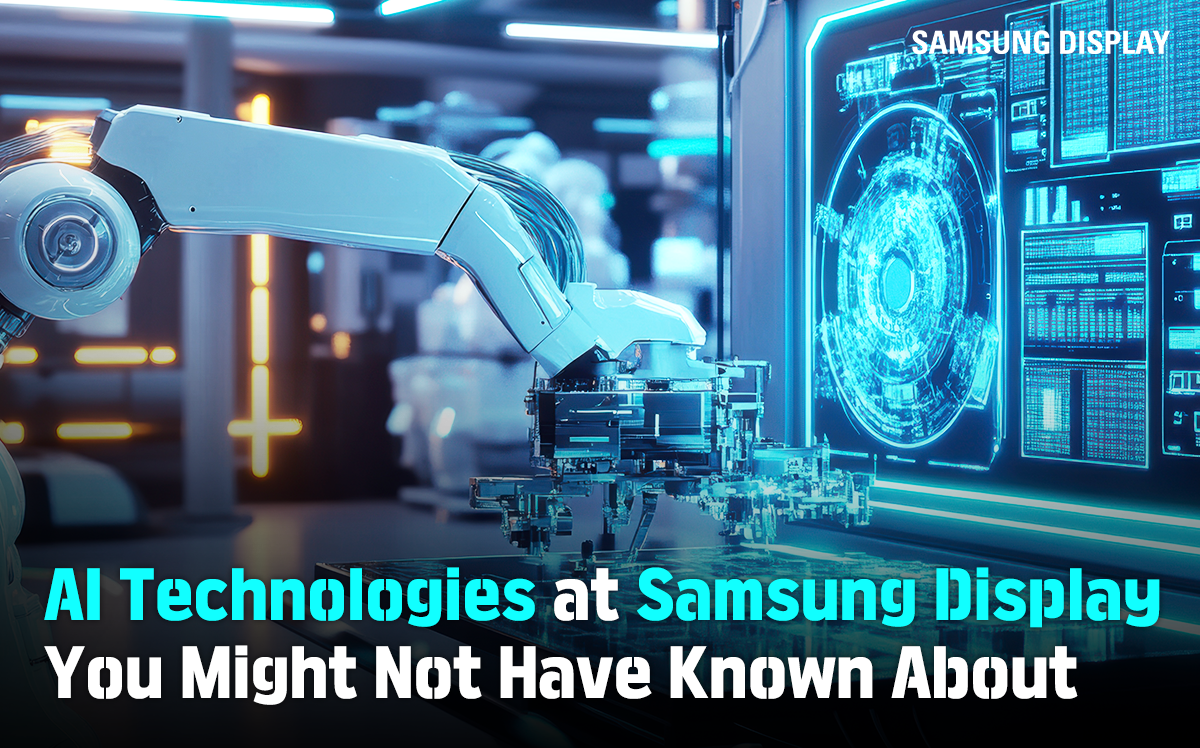
You’ve probably noticed the recent trend — using GPT-4o’s image generation feature to transform your own photos into famous animation styles like those of Ghibli or Disney. It has become a global sensation, to the point where Sam Altman, CEO of OpenAI, remarked that “Our GPUs are melting." As AI technology becomes increasingly familiar to the general public, it is also driving groundbreaking innovations across businesses and industries through AI Transformation (AX).
*AI Transformation (AX): The process by which companies leverage AI to fundamentally reshape industries, automate repetitive tasks, and ultimately maximize industrial productivity.
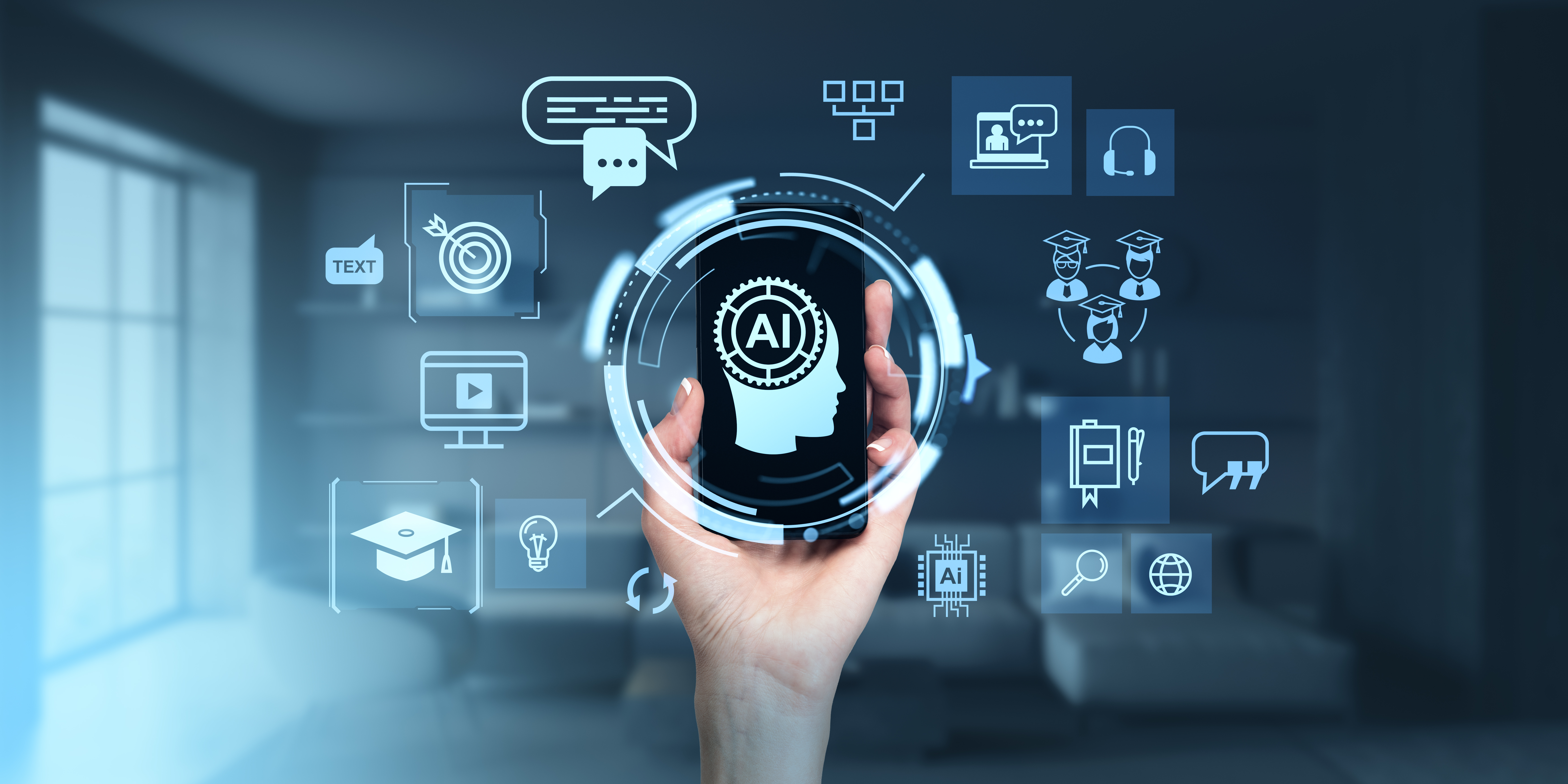
According to the global market research firm, Markets and Markets, the AI market size in the manufacturing sector is projected to grow from USD 3.2 billion in 2023 to USD 20.8 billion by 2028, with a compound annual growth rate (CAGR) of 45.6%. Many manufacturing companies are already adopting AI to reduce production costs and enhance product quality. AI is no longer merely an emerging technology — it is rapidly becoming an essential capability for boosting competitiveness in manufacturing.
So, how is AI being utilized in the display industry? Samsung Display is integrating AI technologies across both its manufacturing processes and research and development activities. Let’s take a closer look at some of Samsung Display’s groundbreaking AI innovations.
Generative AI Technology Used for Masterpiece-Style Image Synthesis — Now Applied to Displays!?
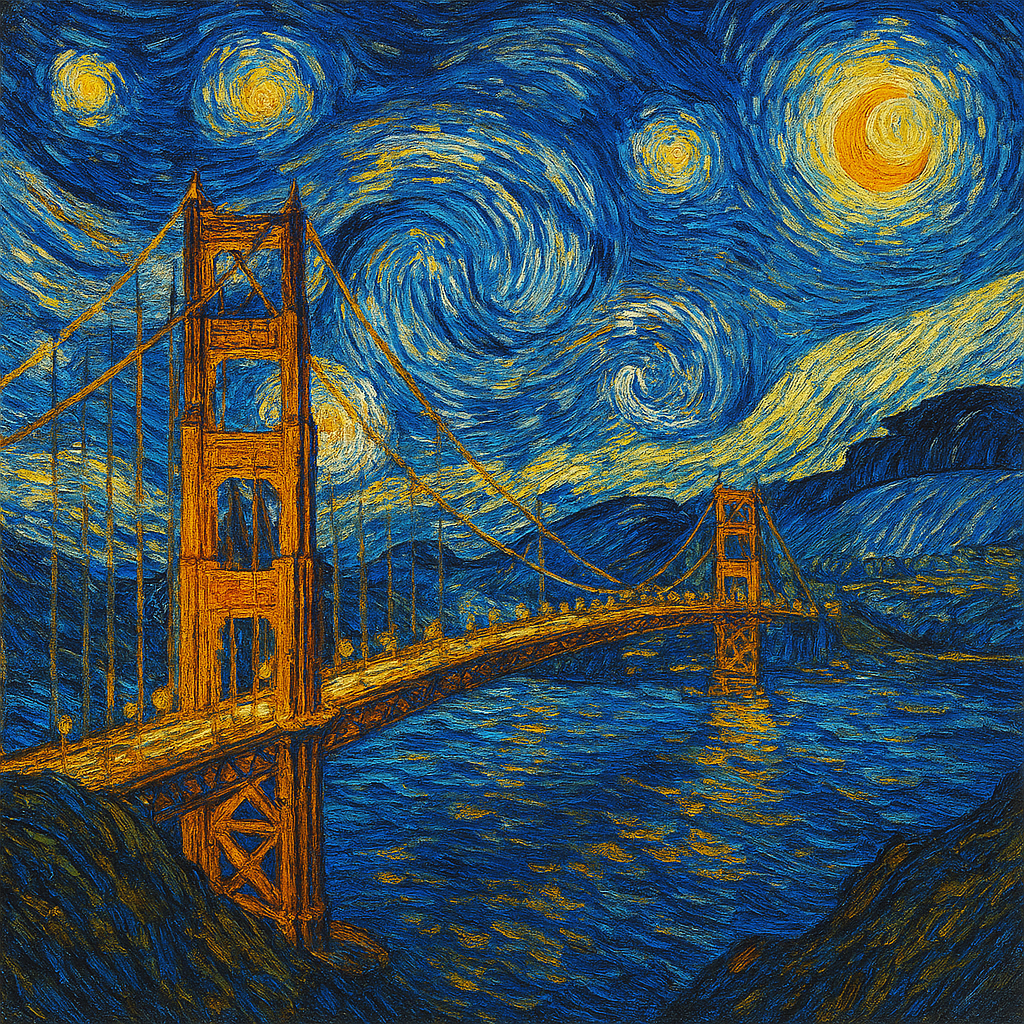
The image of the Golden Gate Bridge, which seems to be looked somehow familiar to us, is a virtual image that is blended with Van Gogh’s Starry Night. This virtual image was generated using a generative AI technique called Neural Style Transfer.
In 2023, Samsung Display became the first company in the world to apply the Neural Style Transfer algorithm to the display industry in critical dimension (CD) measurement, developing a Virtual Image-Based Measurement Technology. This innovation enabled the generation of virtual panel images required for measurement without the need for complex processes.
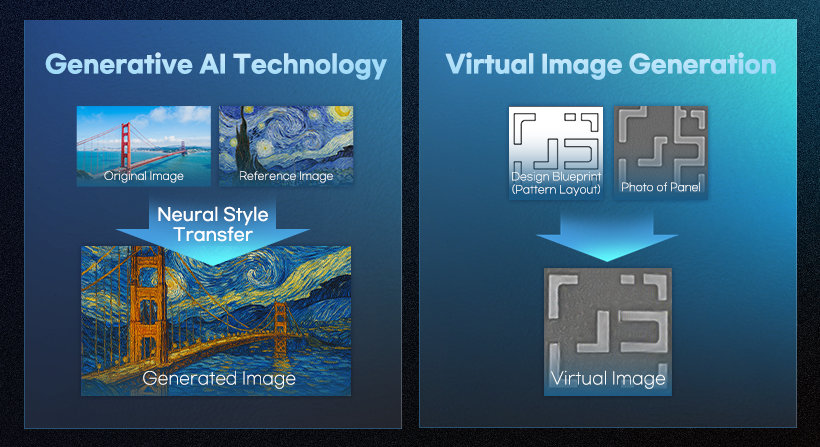
When developing OLED panels, a reference sample is required to verify whether circuit patterns have been fabricated exactly according to the design. Traditionally, a separate production process was necessary to create a standard sample, which was then photographed. The electrode widths were precisely measured and later compared to panels produced afterward — at exactly the same locations.
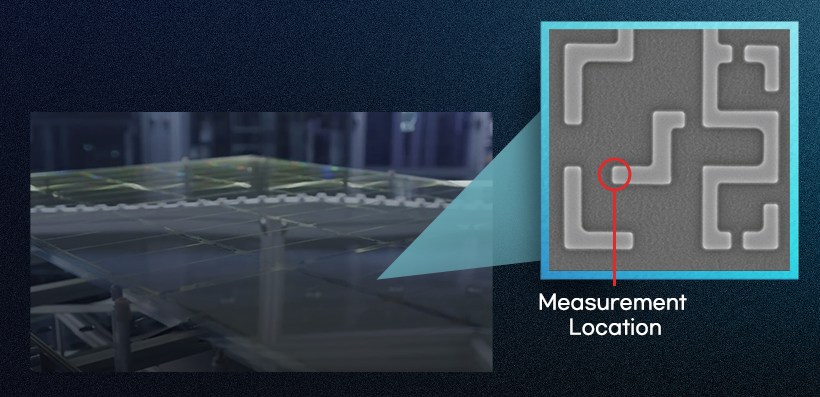
After adopting generative AI, it became possible to easily compare electrode widths across panels using AI-generated virtual images without the need for separate manufacturing processes. By extracting pattern layout images from the design blueprints and combining them with previously developed panel images, virtual images could be generated.
As a result, there was no longer a need to separately process glass substrates just to obtain reference circuit pattern photos, significantly shortening the development timeline and reducing overall manufacturing time.
Simplifying Equipment Setup with AI Technology: Automated Measurement Software!
The "Automated Measurement Software" currently in use at Samsung Display’s Vietnam site leverages AI to shorten equipment setup times. In the display panel production process, it is crucial to conduct accurate and precise measurements during equipment setup to minimize defects and errors during manufacturing.
Previously, workers had to manually carry measurement devices and tablets to perform inspections, which led to several challenges. Mistakes occurred due to human error, and measurement variations were common depending on the operator. There were also safety risks associated with physically accessing the equipment. Moreover, ensuring accurate measurements consumed a significant amount of time.
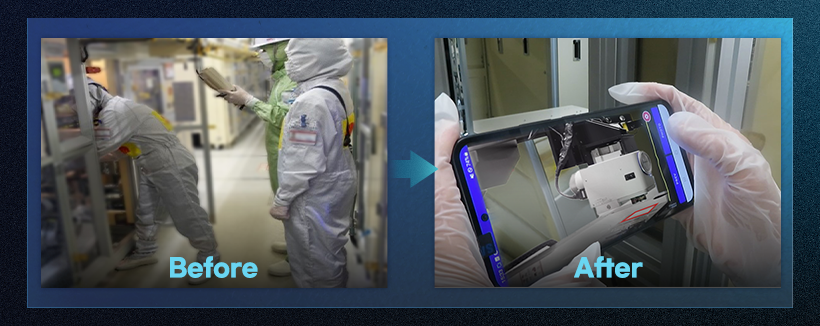
To address these issues, Samsung Display developed the "Automated Measurement Software" incorporating AI technology. This system was designed to streamline the cumbersome measurement process into a single, efficient step. By simply capturing images of the equipment with a mobile device, the AI automatically identifies and extracts the measurement areas, providing workers with measurement results effortlessly.
For example, consider the case of measuring the distance between a picker - the device that lifts the panel - and the panel itself. When a worker captures an image of the entire equipment area with a mobile device, the AI automatically recognizes the picker and the panel within the complex equipment and extracts them as an image model. The AI then calculates the shapes and dimensions of the equipment and panel, automatically measuring the distance and delivering the results to the worker.
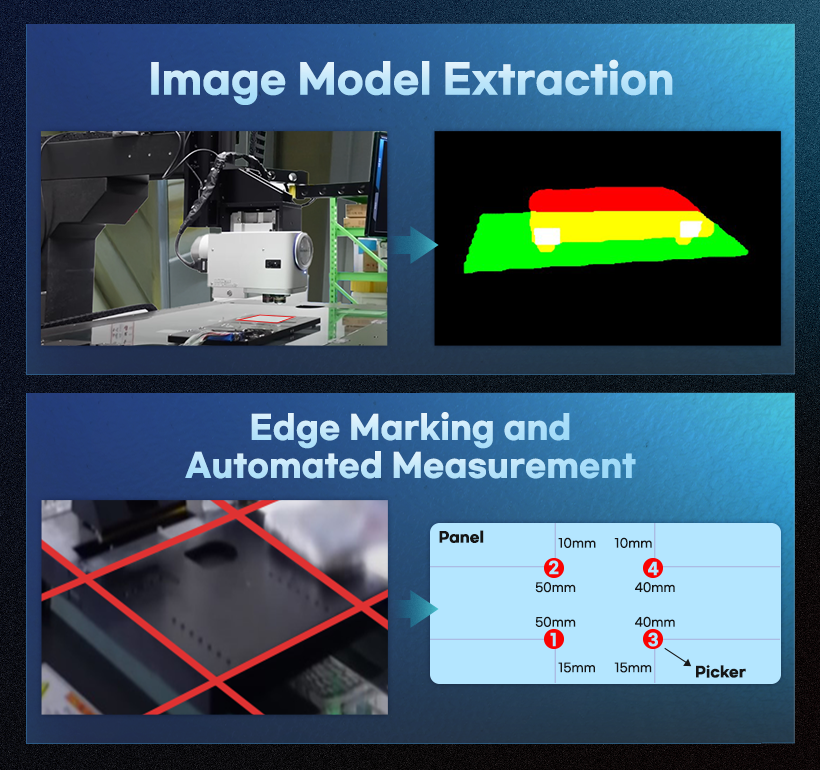
By utilizing AI, necessary components can be selectively extracted even in complex environments, thereby creating a more efficient working environment. As a result, the time required for workers to inspect equipment was drastically reduced from 2 minutes and 30 seconds to just 10 seconds, and thanks to the AI-based systematic approach, measurement errors were significantly minimized.
AI Swiftly Designs New Materials on Its Own~!
AI technology is now playing a critical role even in the material design process for displays. The efficiency and lifespan of organic materials significantly impact overall performance. Thus, finding optimal organic material structures to achieve the desired performance is crucial — but traditionally, it has been a highly time-consuming process.
Samsung Display has developed a system that uses generative AI to simulate an astronomical number of possibilities and identify the optimal material structures. This system is composed of three AI models: Molecule Generation AI, Property Prediction AI, and Synthesis Prediction AI. When engineers input basic molecular structures and target properties, the AI independently learns from simulation and experimental data to generate optimal new molecular structures.
Previously, to design new materials, engineers had to manually modify molecular structures and search for results that closely matched the target values. They had to design countless molecular structures one by one, evaluating each through experiments — an extremely labor-intensive and time-consuming process. Due to the sheer scale of the task, only a limited amount of work could be completed within a month.
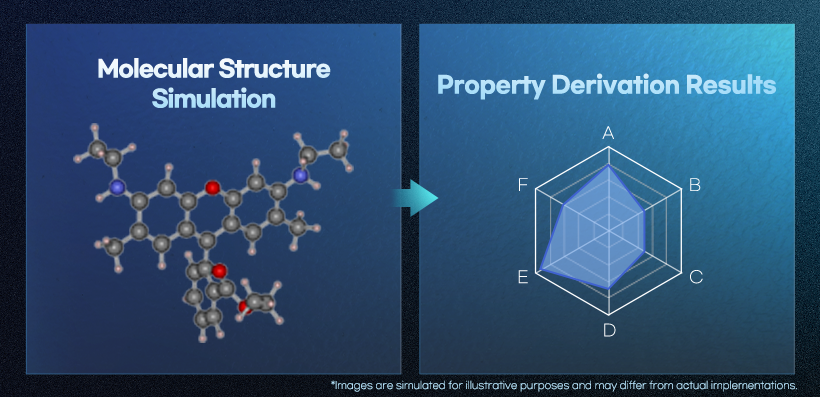
Since adopting the generative AI-based material design system, Samsung Display can now design millions of new organic material structures each month, dramatically improving operational efficiency.
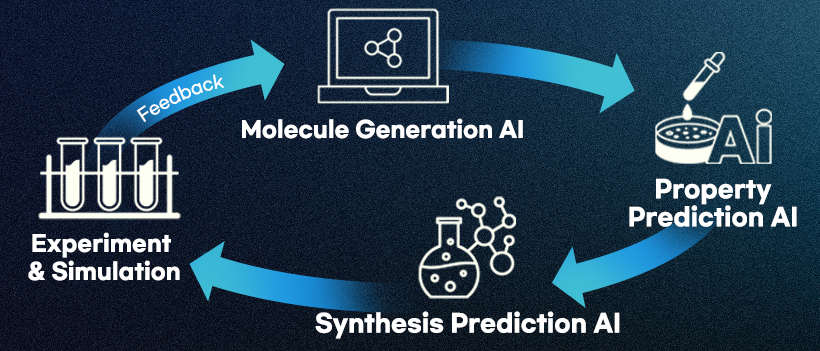
AI technology is now overcoming previous limitations and driving innovation as a new growth engine in the display industry. It is playing an increasingly central role not only in manufacturing processes but also in research and development. As AI technology continues to advance, even more innovative methods and technologies are expected to emerge in the display sector. Stay tuned for Samsung Display’s journey of rapid growth and innovation powered by AI!