Samsung Display’s OLED production line consists of cranes that are 7-8m high, which can experience dust accumulation along the rails, causing display quality issues. As an effort to improve both safety and efficiency, Samsung Display has developed its very own crane cleaning robot.
Meet the developers who built the cleaning robot from scratch: Woohyun Jung and Gwangdon Park from Samsung Display’s Equipment Innovation Team.
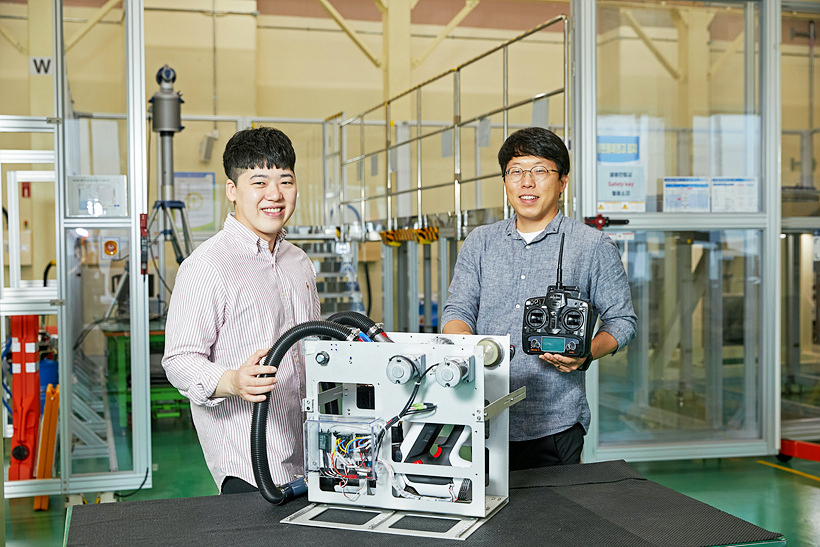
Q: Can you explain the specifics of this cleaning robot?
Woohyun: It’s a robot that cleans the rails of the cranes on our OLED display production line ceilings. Let’s start by understanding what the cranes do. In our display production lines, much of the equipment is big and heavy. Cranes do a better job than humans when it comes to maintaining these machines, and just like the rails on train tracks, rails on the facility ceilings control the movement of these cranes. Of course, dust gathers over time, and using our robot, we can clean the rails remotely.
Gwangdon: Dust accumulation can have a direct impact on our product quality if we’re not consistent with our maintenance. It’s of high importance to us to keep a clean environment since our display production process works on a micro-level.
Q: Was it really necessary to build a robot yourself despite existing methods of cleaning?
Gwangdon: We’ve always cleaned the cranes but they were done manually. Cleaners would hop on ladder-like lifts and brush off any dust on the rails with a cleaning cloth. However, these are tall fixtures and not the easiest places to clean.
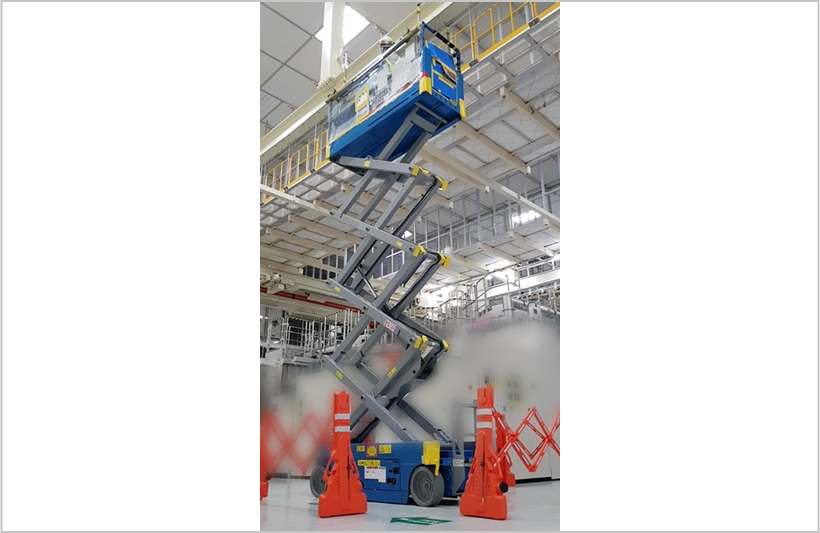
Woohyun: The manual method of cleaning involved at least two cleaners and one safety specialist, which means a team of at least three workers would use the facility lifts to reach rails 7-8m high and clean dust by hand. Because cleaners cannot move the lift when it’s extended, they have to finish cleaning, get off the lift, move the lift, climb up, clean at arms reach and repeat this process. As you can imagine, it can be an arduous process with workers repeatedly going up and down as the lift moves incrementally for cleaning just a single rail. With the development of our robot, we have drastically reduced time spent on this strenuous work as well as improve safety in our facilities.
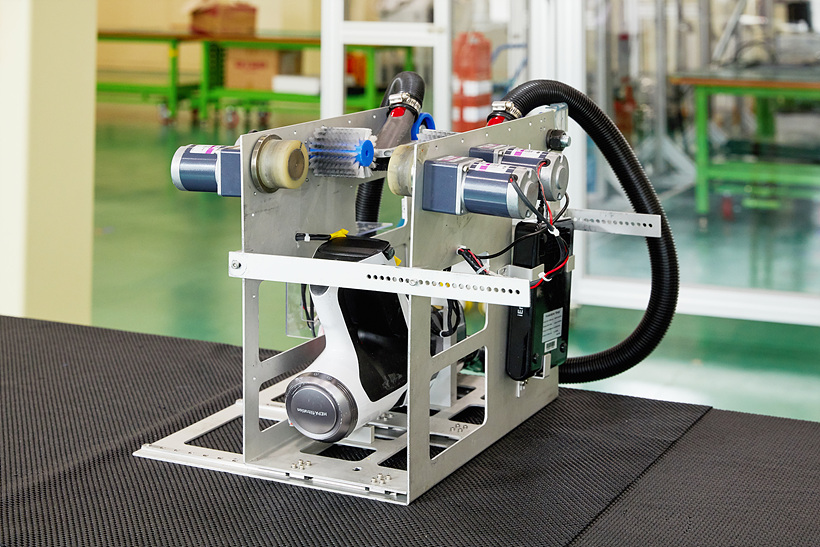
Q: What is unique about this cleaning robot?
Woohyun: There are so many beneficial factors about this robot, but there is a significant value in that we improved safety standards. When you’re working at heights, you face a lot of dangerous situations. Imagine the lift accidentally bumping into other facility devices, cleaners dropping cleaning tools or even falling 7-8m high. Implementing robots can provide a safer working environment.
Gwangdon: I’d like to highlight the fact that we’ve reduced time spent on cleaning down to one quarter of that accomplished with manual work. Now we simply spend time installing/uninstalling the robot on the rails and let it clean the rails in one-go. The robot is also able to reach areas where lifts couldn’t previously, improving the overall performance of our cleaning efforts as well.
Q: What inspired you to come up with this invention?
Woohyun: I’ve actually controlled the lifts and cleaned the rails myself before. When you’re up 7-8m high, you experience anxiety even with the slightest trembles of the device your life depends on. Having to move the lift every other minute also felt inefficient, not to mention long hours being spent by a group of people. Questioning the validity of the existing method led us to explore different ideas to improve efficiency, cost and safety. This was the starting point of our robot development, and it wasn’t long until my colleague Gwangdon and I started sharing plans and sketching out our concepts. I took charge of product concept and specification by sketching, developing, and testing the cleaning robot. Gwangdon took over the later process of integrating the product into cranes, designing the structure for external installation, and finalizing the robot development procedure.
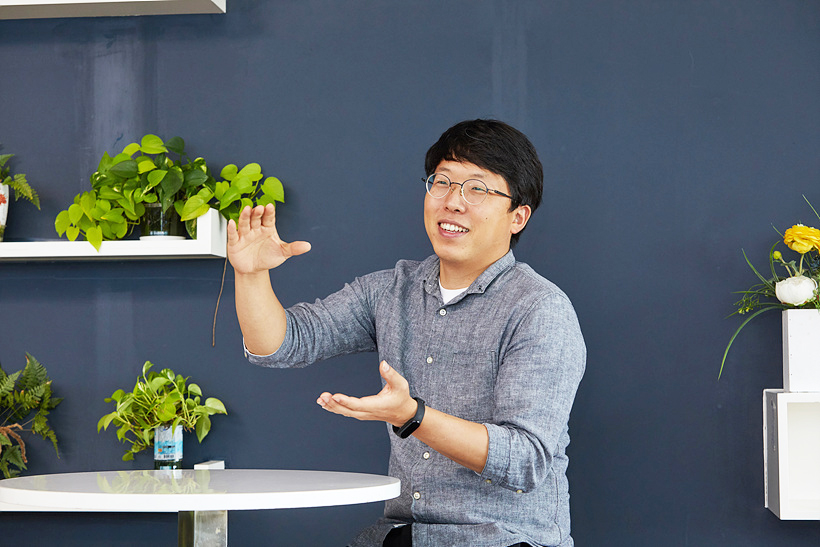
Q: What drove your passion to develop it instead of leaving it as an idea?
Woohyun: We simply couldn’t ignore our instincts to change the norm - we knew all too well what workers experience onsite and the importance of safety in our production lines. Since we were inventing something unprecedented, there was no reference to look up or components built for this use, which meant we had to make everything from scratch ourselves. It was difficult no doubt, but with the emotional and financial support of our team leader, we were able to test out compatibility of different materials and finalize the development process smoothly.
Q: What was the focal point for developing this cleaning robot?
Gwangdon: There were two main goals. First of all, we wanted to ensure that we achieve cleaning efficiency as well as work safety. In our initial attempts, we designed based on the suction power of vacuum cleaners, but it wasn’t enough to clean hardened particles. That’s when we had an epiphany of integrating roller heads found on some vacuum cleaners. We were able to enhance the robot’s capabilities by adding a rotating brush on the front. Safety was another key aspect to our development, making sure that the robot or any of its components don’t fall/fall apart. We even took careful safety considerations in case it does fall to secure extra stability against workplace injuries or fatalities.
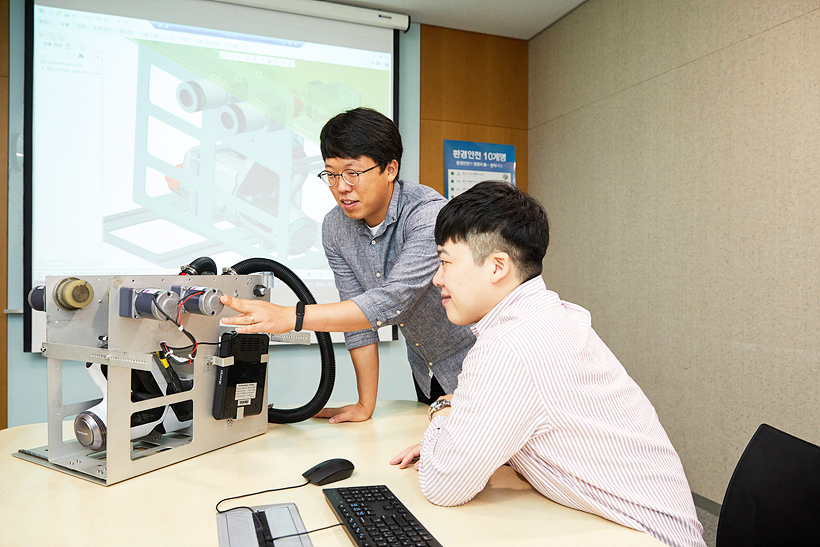
Q: What was the most challenging part technically?
Gwangdon: Getting the cleaner to work remotely was not easy. At first, we reviewed various methods using different control modules and programming, but as our work progressed, we came to realize that we also had to meet network and security standards within our production lines. There was a lot on our plate. I liked playing with remote control cars as a hobby and suggested integrating the RC technology into our efforts. However, we still faced a lot of barriers with this idea. We had to control everything about the cleaner (ex: On/Off, changing modes, etc) remotely while also enabling the various movements involved with the cleaner’s mobility such as speed and drive. Problem was that things weren’t exactly working the way we planned for since we were building something completely new in the industry. We reach out to other experts for advice and endured every trial and error until we were finally able to optimize our design with a final product with features we envisioned.
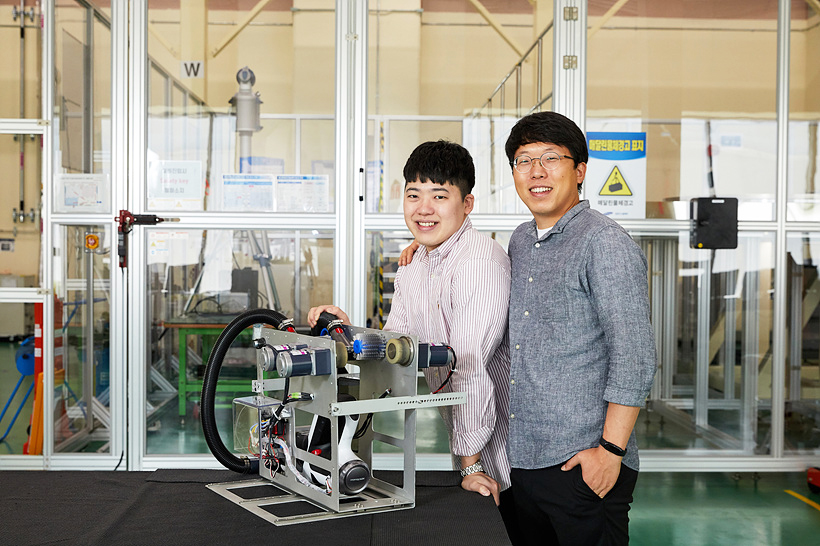
Q. What were your initial thoughts when the company first implemented the robot on site?
Woohyun: My heart was beating out of my chest to be honest since I was worried about unexpected emergencies or less efficient outcomes compared to previous methods of cleaning. I was only able to calm down once the cleaning robot finished its testing safely.
Gwangdon: It’s exhilarating to watch the robot in action, knowing that we’ve realized innovations in improving worker safety and work hours. Not to mention feeling accomplished for having invented something completely new through our experience! We are already jumping into other ideations to secure safety and minimize pain points onsite, as well as develop related products in the near future.